Post Date:5,Feb,2025
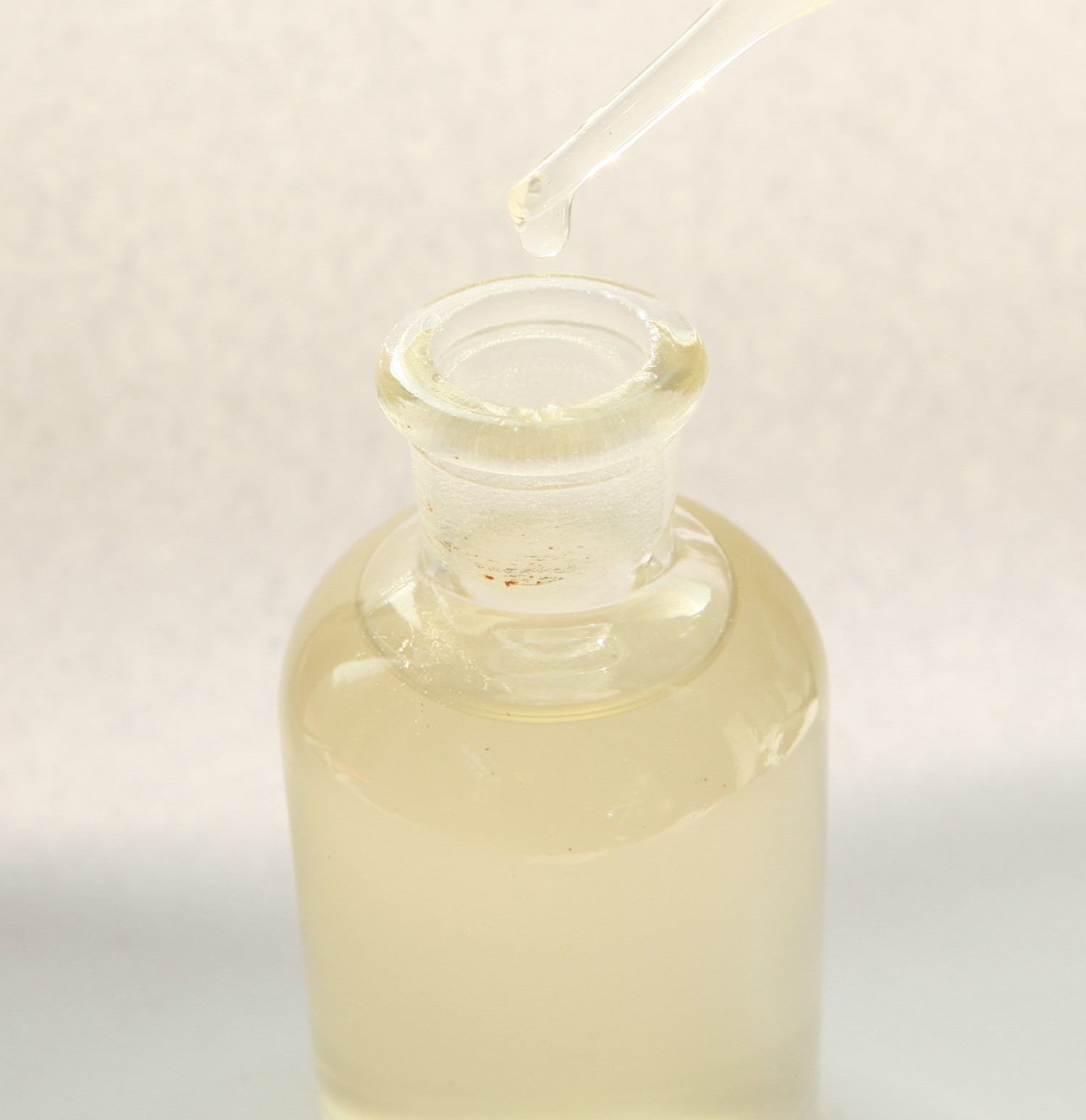
In recent years, high-rise buildings have developed faster and faster, and pumped concrete construction has higher and higher requirements for the cohesiveness, water retention and stability of ready-mixed concrete. In order to meet the construction requirements of high-rise building pumped concrete, ready-mixed concrete companies are forced to have higher and higher requirements for ready-mixed concrete raw materials. Therefore, in recent years, the application of polycarboxylate superplasticizer admixture has become more and more common, gradually replacing the application of naphthalene admixtures in ready-mixed concrete technology. However, although polycarboxylate superplasticizer admixture solves the requirements of high-rise pumping and durability of ready-mixed concrete, polycarboxylate superplasticizer admixture is very sensitive to fluctuations in concrete raw materials and environmental conditions, resulting in various problems in the construction of ready-mixed concrete. For example, the slump of ready-mixed concrete has increased, especially in winter, this phenomenon is more common, and the ready-mixed concrete mixing station is always vaguely solved.
The reasons are analyzed as follows:
1. It is determined by the nature of the molecular structure functional group of the polycarboxylate admixture itself. Under low temperature environment, the speed of cementitious material particles adsorbing polycarboxylate superplasticizer admixture molecular functional groups is slow, and the concrete out of the machine cannot truly reflect the water reduction rate of polycarboxylate superplasticizer admixture. After the transportation time, polycarboxylate superplasticizer admixture fully plays a role, resulting in the slump of concrete on site to increase or even segregate;
2. In winter, steam or electric heating is generally used to heat the mixing water during production at the mixing station. However, the water flow rate is fast during the production process, and the rising temperature of the heated water cannot keep up, resulting in a large difference in the temperature of the mixing water for the front and rear vehicles, which affects the adsorption time of the admixture molecules and cementitious material particles, and thus affects the change of concrete slump;
3. Due to the large production volume of concrete at the mixing station, in order to meet the supply demand, the mixing time of the concrete is shortened, resulting in the slump of the concrete out of the machine is not a true reflection of the polycarboxylate superplasticizer admixture.
Solutions:
(1) Conduct compatibility tests on polycarboxylate superplasticizer admixture and the cementitious materials used in advance to ensure that they meet not only the water reduction rate requirements but also the workability requirements of concrete;
(2) Try to minimize the temperature change of the mixing water used in the mixing station. If conditions permit, set up two water tanks for alternating heating;
(3) Extend the mixing time to ensure that the polycarboxylate superplasticizer admixture and cementitious material particles have sufficient contact time;
(4) Adjust the mix ratio to increase the stability of the concrete and reduce the amount of admixtures to reduce coagulation.
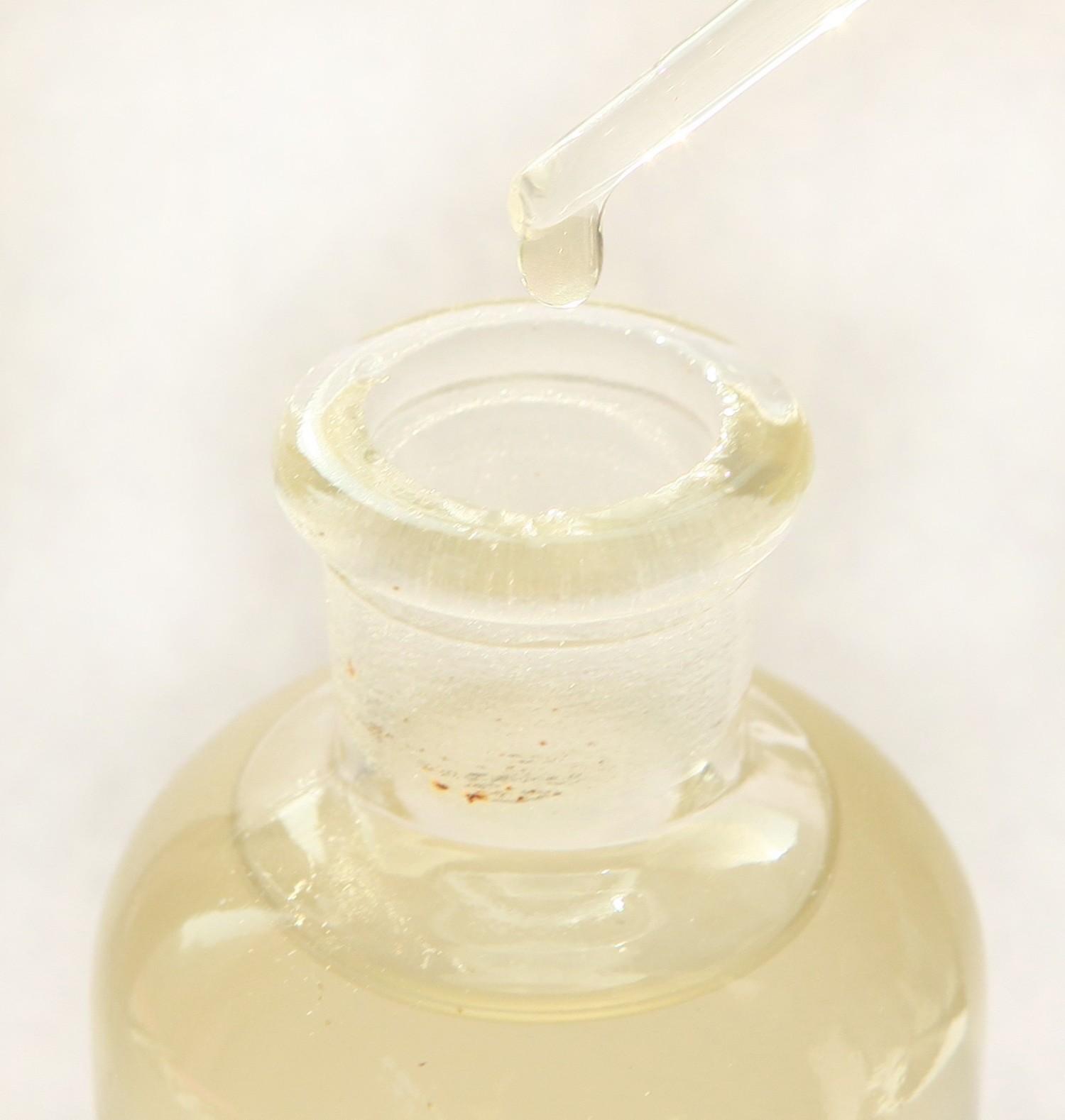
Post time: Feb-19-2025